Safety Issues Relating to Class 4 Laser Welders and Cleaners
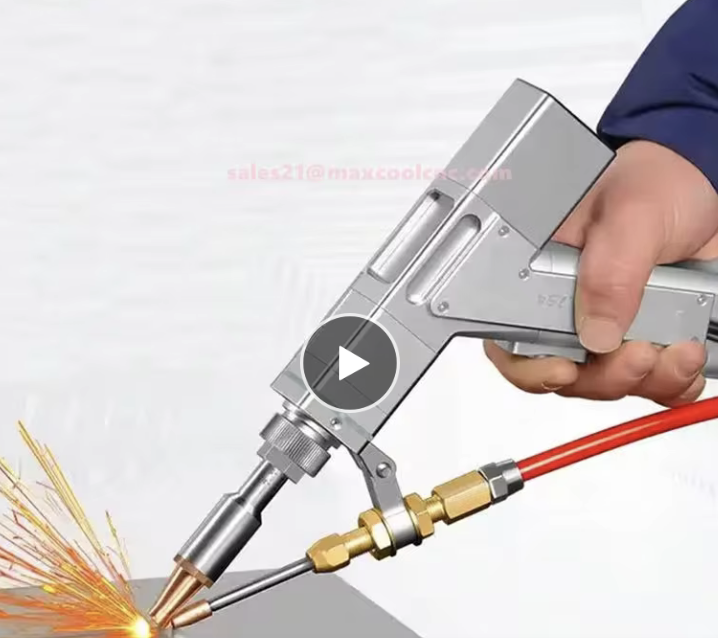
Having personally tested and sold one of these new machines, I’m pleased to report that customer feedback has been overwhelmingly positive. The welder is incredibly user-friendly, even on materials like aluminium, offering high-speed performance with minimal distortion. The refinishing needed on components is minimal.
That said, there are critical safety concerns that must be addressed when using these laser systems. These considerations apply not only to welding but also to laser cutting and cleaning. I have outlined the key safety issues below, but will cover laser cleaning in more detail in a future post.
Safety Issues Relating to Class 4 Laser Welders and Cleaners
Class 4 lasers are the most powerful classification of lasers, encompassing devices used for welding, cutting, and cleaning in industrial settings. These lasers can pose significant hazards if not handled correctly, making strict safety protocols essential. Below are key safety issues and considerations when dealing with Class 4 laser welders and cleaners:
1. Eye Hazards
Direct and Reflected Beam Exposure: Class 4 lasers can cause severe eye injuries, including permanent blindness, through direct or even indirect exposure (like reflections off surfaces). The high intensity of these lasers can damage the retina, leading to immediate or progressive vision loss.
Appropriate Eye Protection: Wearing certified laser safety goggles is crucial. These goggles should be rated for the specific wavelength of the laser in use. Standard eyewear is not sufficient as it does not provide the necessary level of protection.
2. Skin Hazards Burns and Tissue Damage:
Class 4 lasers can burn the skin on contact, with the potential for both superficial and deep tissue injuries. Even brief exposure can result in serious burns, making it vital for operators to use protective clothing and handle the equipment with care.
Flammability Concerns: The beam can ignite flammable materials, posing risks of fire or explosion in environments where volatile substances are present.
3. Airborne Contaminants
Laser-Generated Airborne Contaminants (LGACs): During laser welding and cleaning, the high-energy beams vaporize materials, creating hazardous fumes and particles. These contaminants can include toxic metals, plastics, or other hazardous substances that pose inhalation risks.
Ventilation Systems: Proper exhaust systems and air filtration are necessary to remove harmful particulates and gases from the workspace. Local exhaust ventilation (LEV) systems should be in place to capture fumes at the source.
4. Non-Beam Hazards
Electrical Risks: Laser systems require high-voltage power supplies, posing risks of electrical shock or fire. Regular maintenance, proper grounding, and adherence to electrical safety standards are essential.
Mechanical Hazards: Moving parts, such as robotic arms or rotating components in laser systems, can cause mechanical injuries if operators are not vigilant.
5. Operational Safety and Training
Training and Certification: Operators must be adequately trained in the safe use of Class 4 lasers, including understanding the specific risks associated with the device they are handling. They should be certified in laser safety protocols and have a comprehensive understanding of emergency procedures.
Controlled Access and Safety Interlocks: Class 4 laser operations should be confined to designated areas with restricted access. Safety interlocks and emergency stop buttons should be integrated into the laser system, preventing unauthorized use and enabling quick shutdown in case of an emergency.
6. Reflective Surfaces and Beam Path Control
Control of Reflections: The beam from a Class 4 laser can reflect off surfaces like glass, polished metal, or even unintended areas, causing harm. It is crucial to control the laser's path and avoid working near reflective materials unless the environment is specifically designed to manage them.
Beam Enclosures and Barriers: Where possible, enclosures and barriers should be installed to contain the beam and reduce the risk of accidental exposure.
7. Emergency Procedures and Signage
Clear Signage: Areas where Class 4 lasers are used should be marked with appropriate warning signs indicating laser hazards. Laser hazard zones should be clearly defined, and access should be restricted when the laser is in operation.
Emergency Response Plans: A well-defined emergency response plan, including first-aid measures for laser injuries, must be in place. All personnel should be familiar with shutdown procedures, and emergency contact information should be readily available.
Conclusion
Class 4 laser welders and cleaners are powerful and versatile tools that significantly enhance industrial processes but come with considerable safety risks. Comprehensive safety protocols, proper training, and the use of protective equipment are non-negotiable when operating these devices. By addressing these safety concerns and implementing robust safety measures, workplaces can mitigate the risks associated with Class 4 lasers and ensure a safer environment for operators and nearby personnel.